Die Blackstone Technology GmbH, eine Tocher der Blackstone Resources AG, wird im sächsischen Döbeln eine Pilot-Batteriezellproduktion für Natrium-Ionen-Batterien installieren. Das gab der börsennotierte Konzern aus der Schweiz am 28. März in einer Ad hoc-Mitteilung bekannt.
BMWI fördert Festkörperbatterie-Forschung
In die Weiterentwicklung und Skalierung der Produktion der Batterien sollen laut Blackstone rund 32 Millionen Euro in Döbeln investiert werden. Bis zu 24,1 Millionen Euro der Investitionssumme soll dabei aus Fördergeldern des deutschen Bundesministerium für Wirtschaft und Klimaschutz gedeckt werden. Die Pilotanlage in Döbeln soll dabei die Vorarbeit leisten, um ab dem Jahr 2025 solche Batterien im großen Maßstab produzieren zu können.
Beteiligt an dem Projekt in Döbeln ist das Berliner Unternehmen Eurabus, das die gefertigten Batterien in einem Elektrobus einsetzen wird. In der Forschung und Entwicklung arbeiten außerdem die Fraunhofer-Institute IFAM, IKTS, IST und das Institut für Partikeltechnik der TU Braunschweig sowie das Unternehmen Zeiss mit.
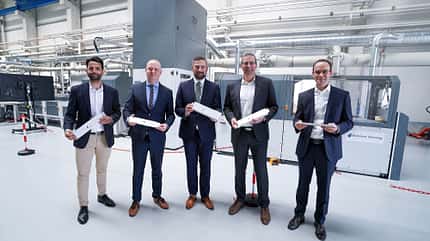
"Die Natrium-Ionen-Technologie stellt die nächste Generation unserer bereits heute marktführenden 3D gedruckten Batterien dar", so Holger Gritzka, CEO der Blackstone Technology GmbH. "Wir freuen uns, damit erneut einen innovativen und tragfähigen Beitrag zu sauberer Energie und dem kohlenstoffneutralen Verkehrswesen der Zukunft zu leisten."
Günstiger und umweltfreundlicher
Das chemische System der Natrium-Ionen-Batterien ist in Teilen mit Lithium-Ionen-Zellen vergleichbar. Ein wesentlicher Vorteil von Natriumbatterien ist, dass Rohstoffe bei vergleichbarer Technologie deutlich einfacher und umweltschonender zu gewinnen sind. Die Verfügbarkeit von Natrium ist gegenüber Lithium um ein Vielfaches höher und der Preis deutlich niedriger. Ausserdem muss der Rohstoff nicht wie Lithium aus dem außereuropäischen Ausland importiert werden.
Die 3D-Druck- und Festkörperbatterietechnologie von Blackstone Technology bietet laut Angaben des Unternehmens erhebliche Vorteile gegenüber herkömmlichen Batteriezellendesigns, die flüssige Elektrolyte verwenden. Sie ermöglicht niedrigere Kosten in der Produktion, erhöht die Energiedichte der Zellen und bietet eine höhere Anzahl von Ladezyklen. Angestrebt sind Produktionskosten von unter 65 US-Dollar pro kWh. Laut einer Analyse des Forschungsinstituts BloombergNEF lagen die Produktionskosten für E-Auto-Akkus im Jahr 2021 auf Zellebene bei durchschnittlich 97 US-Dollar pro kWh.