Bereits vor etwa 25 Jahren verwendete Chevrolet in der Corvette C5 vorn und hinten Querblattfedern aus glasfaserverstärktem Verbundwerkstoff (GFK). Da eine Feder teilweise zu den ungefederten Massen gehört, verringerten die Leichtbaufedern diese. So verbessert sich nicht nur der Fahrkomfort, auch die Fahrsicherheit der Corvette profitiert von der geringeren ungefederten Masse.
Gegenüber Stahlfedern wiegen glasfaserverstärkte Federn wesentlich weniger: Die Dichte von GFK ist etwa viermal geringer als die von Stahl. GFK ist korrosionsbeständig. Das ist vorteilhaft, weil die Federn unter dem Auto starker Feuchtigkeit – und vor allem im Winter hohem Salzgehalt – ausgesetzt sind. Da keine Rostnarben entstehen, kann sich auch kein Dauerbruch durch lange Wechselbelastung entwickeln. Die Stahlfeder würde bei zunehmender Korrosion am Ende plötzlich versagen und brechen. Der GFK-Versagensmodus ist komplett anders als bei Stahl. GFK verliert seine Steifigkeit nur langsam. Das Bauteil zerbricht nicht in mehrere Teile.
Federn aus Kunststoff oder GFK können in nahezu jeder Form hergestellt werden, es bestehen viel mehr Möglichkeiten, eine Federform zu gestalten. Zudem sind Federn aus Kunststoff nicht elektrisch leitend.
Eigenschaften von GFK
Glasfaserverstärkte Kunststoffe bieten ein enormes Leichtbaupotenzial, da die spezifischen, also die auf die Dichte bezogenen, Werkstoffkennwerte Zugfestigkeit zu Elastizitätsmodul in Faserrichtung gegenüber anderen Konstruktionswerkstoffen ein vorteilhaftes Verhältnis ergeben. Somit ist das Material höchst flexibel bei gleichzeitig höchster Bauteilfestigkeit bei geringerem Gewicht. Wird dieser Werkstoff für Blattfedern eingesetzt, können diese Leichtbau-Eigenschaften bestmöglich ausgenutzt werden. Dies gelingt immer dann, wenn die Feder primär auf Zug, Druck oder Biegung belastet wird. So kann ein unidirektionaler Lagenaufbau umgesetzt werden: das heißt, die Fasern sind ausschließlich in die Haupt-Belastungsrichtung der Blattfeder orientiert, und die Belastung wird im Wesentlichen durch die hochmoduligen und hochfesten Glasfasern aufgenommen.
Die vergleichsweise niedrigmodulige und feste Matrix stützt die Fasern und ermöglicht eine gleichmäßige Krafteinteilung in die Fasern. Zudem korrodieren GFK-Federn nicht, und sie zeichnen sich durch ein gutmütiges Versagensverhalten ("Fail-safe Behavior") in Form eines langsamen Steifigkeitsverlustes aus.
Die GFK-Blattfeder
Die Mubea Fahrwerksfedern GmbH mit Hauptsitz in Attendorn entwickelt seit 2008 und fertigt seit 2016 GFK-Blattfedern für die Automobilindustrie in Serie. Der Federproduzent arbeitet mit allen namhaften Herstellern von Fahrzeugen, bei denen Blattfedern eingesetzt werden, in Serienapplikationen und in mehr oder weniger seriennahen Entwicklungsprojekten zusammen. Dazu gehören OEMs aus Europa, Nordamerika und Asien. Mubea fertigt sowohl Längs- als auch Querblattfedern, wobei die Längsblattfedern in konventionelle Blattfedern (BF) und die patentierte Blattzugfeder (BZF) unterschieden werden. Die Querblattfedern (QBF) wiederum werden in drei unterschiedliche Funktionsintegrationsstufen eingeteilt.
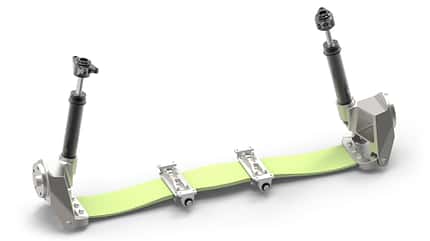
Längsblattgeführte Starr- oder De-Dion-Achskonzepte werden vorrangig in Pickups und leichten Nutzfahrzeugen eingesetzt, mit Gesamtfahrzeuggewichten bis zu 5,5 t. Die konventionelle einlagige Blattfeder aus GFK ersetzt eine Stahlblattfeder 1 : 1, weist eine lineare Federkennlinie auf und ermöglicht Gewichts-Einsparpotenziale bis zu 50 % gegenüber dem Stahlpendant.
Die Blattzugfeder ist eine ebenfalls einlagige GFK-Blattfeder und ersetzt mehrlagige Stahlfederpakete mit multilinearer Federcharakteristik sowie den Schäkel, der bei Stahlblattfedern den benötigten Längenausgleich über der Einfederung ermöglicht. Durch die Integration des Schäkels in die BZF sind beide Federenden fest mit dem Fahrzeugrahmen verbunden und der Längenausgleich über die Einfederung wird verhindert oder lediglich über nachgiebige Federbereiche generiert. Es entsteht ein überbestimmtes System, bei dem sich Biegung und Zugbelastung infolge des gesperrten Längenausgleichs überlagern und somit für eine stetig progressive Kennlinie der einlagigen GFK-Feder sorgen. Durch dieses patentierte System lassen sich bauteilbezogen bis zu 75 % bzw. 30–45 kg pro Fahrzeughinterachse einsparen.
Weitere Vorteile von GFK-Längsblattfedern sind:
► erhöhte Fahrzeugzuladung
► weicher Ratenübergang durch stetig progressive Kennlinie
► Komfortverbesserung
► homogene Aufbaueigenfrequenz
► keine Zwischenlagenreibung
► keine Korrosion
► keine Geräuschentwicklung und unkontrollierte Dämpfung
► verlängerte Lebensdauer
► Teilereduktion.
Schraubenfedern
Konzepte für Schraubendruckfedern aus GFK zeigen ein deutlich geringeres Leichtbaupotenzial, welches auf die unterschiedliche Materialbelastung im Vergleich zur Blattfeder zurückzuführen ist. Die dominante Torsionsbelastung von Schraubendruckfedern muss im Falle von Faser-Kunststoff-Verbunden über einen Lagenaufbau mit wechselnder Faserorientierung realisiert werden. Die limitierende Werkstoffkenngröße ist die vom Matrixwerkstoff gesteuerte Querzugfestigkeit des Verbunds, welche im Vergleich zu faserdominierten Festigkeiten deutlich geringer ausfällt. Erhöhter Bauraumbedarf und verringerte Setzbeständigkeit bringen zusätzliche Herausforderungen mit sich.
Wenngleich mäanderförmige GFK-Achsfedern vorrangig auf Biegung belastet sind und so einige Defizite wettmachen, sind auch hier Querzugspannungen der limitierende Faktor.
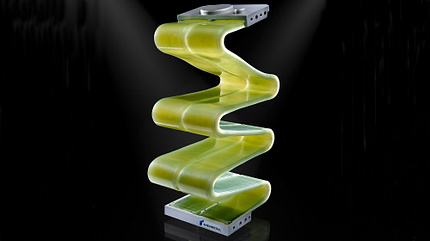
Zu beachten sind darüber hinaus eine aufwendige Schnittstellengestaltung und die verringerte Stabilität der Feder – insbesondere unter höheren Einsatztemperaturen.
GFK-Schraubenfedern wurden bisher allerdings nur bei speziellen High-Performance-Fahrzeugen eingesetzt. Der Audi A6 Avant 2.0 TDI Ultra hatte 2014 solche Federn.
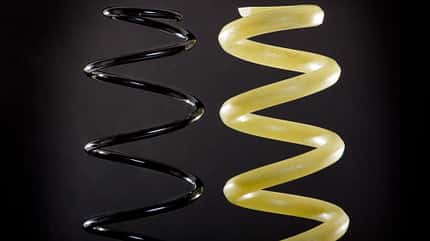
Audi arbeitete bei diesen Federn mit dem spezialisierten Zulieferer Sogefi SpA (Mailand/Italien) zusammen.
Mittlerweile wurde die Feder aber wieder aus dem Programm genommen. Audi-Pressesprecher Udo Rügheimer begründete es mit der fehlenden Wirtschaftlichkeit. Beanstandungen seien keine aufgetreten. "Die Vorteile der GFK-Federn waren für eine breite Serienanwendung nicht groß genug", resümierte Rügheimer den Einsatz dieser Federn.
Eine Mäanderfeder aus GFK besitzt das Mercedes-Versuchsfahrzeug EQXX. Der Leichtbaugedanke wurde hier konsequent umgesetzt, auch weil der Kostendruck gering war. Vielleicht können diese glasfaserverstärkten Kunststofffedern zukünftig Schraubenfedern aus Stahl ersetzen.
Querblattfedern
Abhilfe schaffen Achskonzepte mit GFK-Querblattfedern (QBF), die in verschiedenen Funktionsintegrationsstufen an Vorder- und Hinterachsen in Pkw und Nfz eingesetzt werden können. Mubea unterscheidet zwischen:
► QBF mit Federungsfunktion
► QBF mit Federungs- und Stabilisationsfunktion
► QBF mit Federungs-, Stabilisations- und Radführungsfunktion.
Werden mehr Funktionen integriert, reduziert dies die Anzahl an Achskomponenten. So lassen sich bis zu 15 Kilogramm pro Achse sparen, bei zusätzlich verringerten Kosten.
Eine zweifach flexible innere Lagerung der Blattfeder stabilisiert das Wanken. Neben dem Verlauf der Federkontur dient vor allem die Lagerpositionierung zur Einstellung des angestrebten Ratenverhältnisses aus Huben und Wanken. In Kombination mit zwei radführenden Dämpfern kann eine am Radträger befestigte Querblattfeder auch die Radführungsfunktion übernehmen und somit das konventionelle Mehrlenker-Achssystem, bestehend aus Achsfedern, Stabilisator und Lenkern, substituieren.
Die Einstellung der gewünschten Achskinematik erfolgt im Wesentlichen durch Charakteristik und Positionierung der Lager- und Dämpferelemente. Durch den so entstehenden kompakten Achsaufbau wird insbesondere in Fahrzeuglängsrichtung zusätzlicher Bauraum verfügbar, der beispielsweise für Batteriekomponenten genutzt werden kann.
Mubea verfügt über alle relevanten Fertigungstechnologien für Faser-Kunststoff-Verbunde wie Wickelverfahren, Fertigung mittels Autoklaven, Resin-Transfer-Molding oder dem Prepreg-Prozess. Höchstmögliche Bauteilgüte der GFK-Blattfedern wird mit dem Prepreg-Verfahren erreicht, da der Prozess die größte Designflexibilität bei konstant hoher Materialqualität und leichtbauoptimiertem Materialeinsatz gewährleistet.
Dem Prepreg-Verfahren liegen vorimprägnierte Glasfasern (pre-impregnated fibers) zugrunde, die zu einem geschichteten Federrohling drapiert werden. Dieser Rohling wird mittels Heißpressverfahren in seine finale Form gebracht, wobei überschüssiges Harz herausgepresst wird. Abschließend erfolgen die maschinelle Endbearbeitung, Montage und Funktionsprüfung der GFK-Feder.
Weitere GFK-Federn
GFK, dessen Faserbestandteil Glasfasern sind, ist etwas schwerer als CFK (aus Carbon), aber bei Weitem günstiger herzustellen. GFK-Federn sind durchsichtig und meistens durch das Harz gelblich oder hellgrün gefärbt.
Die Firma SGL stellt die Blattfedern für die Hinterachse des Ford Transit her.
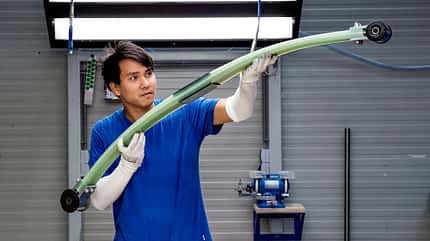
Die Federn kommen in Verbindung mit dem Transit-Tiefrahmenfahrgestell zum Einsatz. Sie werden damit dort eingesetzt, wo es in besonderem Maße auf große Nutzlasten und Zuladung ankommt, etwa in Reisemobilen oder in besonderen Nfz-Varianten des Transit. Im Vergleich zu Stahlfedern ist die Composite-Blattfeder etwa 50 Prozent leichter. Ermöglicht wird der Einsatz unter anderem durch eine 1 : 1-Kompatibilität mit herkömmlichen Federn.
Stabilisatoren aus CFK
Im Porsche 911 GT3 RS mit Weissach-Paket sind Schubfeld, Stabi vorne/hinten und Koppelstange aus CFK. Kohlefaserverstärkte Bauteile sind nicht durchsichtig und haben durch die Kohlefasern eine schwarze Färbung. Das Gewicht wird reduziert und das Handling verbessert.
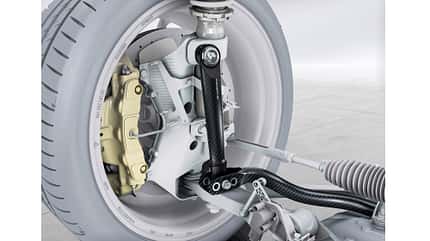
Fazit
Federn sind bislang zum großen Teil aus Stahl, doch im Bereich SUV, Pickup und Transporter setzen sich immer mehr Blattfedern und Blattzugfedern aus glasfaserverstärktem Kunststoff GFK durch.
Leichtere Federn reduzieren die ungefederten Massen, was die Bodenhaftung und damit die Fahrdynamik verbessert, die allerdings bei diesen Fahrzeuggruppen nicht eben im Vordergrund steht. Nur für High-Performance-Fahrzeuge werden Federungsteile wie Stabilisatoren aus CFK verwendet, die zwar sehr leicht sind, aber auch sehr viel teurer als Stahlfedern. Sinnvoll erscheint hingegen die Verwendung solcher GFK-Federn in Elektroautos. So könnte das hohe Gewicht etwas reduziert, somit die Zuladung verbessert werden, und angesichts der ohnehin hohen E-Auto-Preise würden diese Mehrkosten nicht allzu sehr ins Gewicht fallen.
Noch sind die GFK-Federn allerdings exotische Bauteile. Trotz der zahlreichen Vorteile steht bei einer Feder neben ihren Eigenschaften vor allem der Stückpreis im Vordergrund. Und der ist bei Stahlfedern einfach unschlagbar.